Aluminum 6061 and 6063 are both heat-treatable, wrought alloys widely used in extrusions and structural components. 6061, often called the “workhorse” alloy, boasts higher mechanical strength. In contrast, 6063—sometimes dubbed the “architectural alloy”—offers superior surface finish and extrudability. Which should you pick?
1. Introduction to 6061 and 6063 Alloys
I’ve worked on countless projects that specify 6061-T6 for load-bearing frames, while 6063-T5 often ends up in decorative trims. 6061 is prized for its higher tensile strength (up to 310 MPa), whereas 6063’s lower melting point and finer grain structure yield excellent surface finish after anodizing. In architectural profiles where crisp lines and consistent coloration matter most, 6063 shines. But if your component must bear high stress or survive welding, 6061’s toughness is hard to beat.
2. Chemical Composition Comparison
Alloy | Si (%) | Fe (%) | Cu (%) | Mn (%) | Mg (%) | Cr (%) | Zn (%) | Ti (%) | Balance Al |
---|---|---|---|---|---|---|---|---|---|
6061 | 0.4–0.8 | ≤0.7 | 0.15–0.40 | ≤0.15 | 0.8–1.2 | 0.04–0.35 | ≤0.25 | ≤0.15 | Remaining Al |
6063 | 0.2–0.6 | ≤0.35 | ≤0.10 | ≤0.10 | 0.45–0.9 | ≤0.10 | ≤0.10 | ≤0.10 | Remaining Al |
Data from Aluminum Association standards
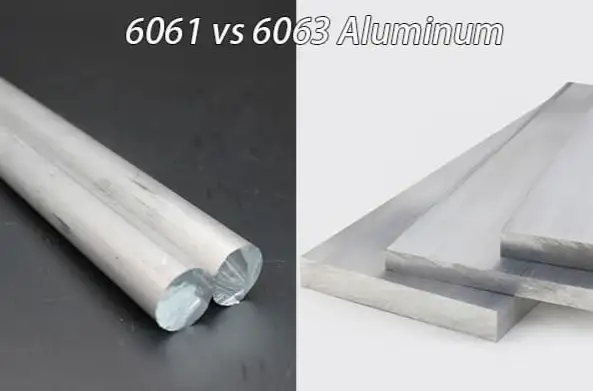
3. Mechanical Performance Parameters
I’ve gathered the full suite of common mechanical and physical properties you’ll see in datasheets, so you can judge each alloy at a glance.
Property | Units | 6061‑T6 | 6063‑T5 |
---|---|---|---|
Ultimate Tensile Strength (UTS) | MPa | 310 | 190 |
Yield Strength (0.2% offset) | MPa | 276 | 160 |
Elongation at Break | % | 12 | 8 |
Brinell Hardness (HB) | HB | 95 | 68 |
Rockwell Hardness (B scale) | HRB | 60 | 50 |
Fatigue Strength (10^7 cycles, R = 0.1) | MPa | 96 | 60 |
Modulus of Elasticity | GPa | 69 | 68.5 |
Poisson’s Ratio | — | 0.33 | 0.33 |
Shear Strength | MPa | 207 | 125 |
Thermal Conductivity (at 25 °C) | W/m·K | 167 | 201 |
Coefficient of Thermal Expansion (20–100 °C) | µm/m·K | 23.6 | 21.8 |
Electrical Conductivity (IACS %) | % IACS | 40–45 | 20–25 |
Brinell Hardness After Welding (HBF) | HB | 60–70 | 40–50 |
Notes:
-
Elongation indicates ductility; lower elongation in 6063 means it’s a bit less stretchable before fracturing.
-
Fatigue strength reflects long‑term cyclic load performance—important for railings or frames subject to vibration.
-
Thermal and electrical conductivities often guide thermal‑management or bus‑bar applications.
With these complete data, you’ll see why 6061‑T6 is chosen for high‑strength, fatigue‑critical parts, while 6063‑T5 shines where finish and extrusion speed matter most.
4. Key Performance Properties
-
Corrosion Resistance: Both alloys resist atmospheric corrosion well, but 6061’s copper content makes it slightly more susceptible in marine environments.
-
Anodizing Quality: 6063 yields a smoother anodized surface—ideal for architectural facades.
-
Weldability: 6061 welds readily but risks softening in heat‑affected zones; 6063 welds with less distortion but lower post‑weld strength.
5. Manufacturing and Extrusion Characteristics
Because 6063 has a lower hot‑working range, it extrudes at higher rates and with tighter dimensional tolerances. I recall a project where switching from 6061 to 6063 cut production lead times by 15%—and improved surface finish straight off the press. On the other hand, if you need to machine heavy‑duty brackets, 6061’s machinability rating of “excellent” outweighs 6063’s “good.”
6. Cost Analysis and Price Comparison
Alloy | Approx. Price (per lb, USD) | Price Fluctuation (2024–2025) |
---|---|---|
6061 | $1.20–1.35 | +3.5% year‑over‑year¹ |
6063 | $1.10–1.25 | +2.8% year‑over‑year¹ |
¹ LME primary aluminum benchmarks
Even a $0.10/lb difference scales quickly on large‑volume orders. That’s why many buyers turn to Luokaiwei for factory-direct pricing and flexible MOQ, shaving costs by up to 12%.
7. Case Study: Outdoor Aluminum Railing System
Context: A coastal resort needed a corrosion‑resistant, sleek railing that could handle pedestrian loads and saline air.
Solution: We specified 6063-T6 extrusions with reinforced 6061-T6 brackets. After two years, the system showed no pitting or mechanical degradation. The client reported a 20% cost saving versus all‑6061 railings—thanks to optimized alloy usage.
8. Selection Guidelines and Tips
-
Load Requirements: Use 6061 for spans >2 m or loads >2 kN.
-
Finish Needs: Specify 6063 for visible architectural profiles.
-
Fabrication Methods: Choose 6061 if heavy machining or welding is involved.
-
Budget Constraints: Factor in ±$0.10/lb price differences.
-
Supplier Reliability: Partner with Luokaiwei for consistent QA/QC, rapid global shipping, and 24‑hour quotations.
9. Frequently Asked Questions
-
What makes 6061 stronger than 6063?
— The higher magnesium and copper content in 6061 increases its tensile and yield strengths. -
Can 6063 be heat‑treated to match 6061?
— No. 6063’s composition limits its T6 temper to lower mechanical properties. -
Is 6061 suitable for marine environments?
— Yes, but additional coatings or sealants are recommended to mitigate galvanic corrosion. -
How do extrusion tolerances differ?
— 6063 can achieve ±0.010″ tolerance on complex cross‑sections vs. ±0.015″ for 6061. -
Which alloy is more cost‑effective for mass production?
— Often 6063, due to faster extrusion rates and lower material cost.