I use aluminum nearly every day, from the airplanes I fly in to the soda cans I recycle. Its combination of light weight, strength, and resistance to corrosion makes it indispensable across sectors. Moreover, its excellent thermal and electrical conductivity extends its reach into power grids and electronics. Therefore, when someone asks “what is aluminum used for,” I immediately think of industries as varied as transportation, construction, packaging, electrical engineering, and consumer goods.
1. Introduction: Defining Aluminum and Its Core Attributes
Aluminum is a silvery-white element (symbol Al; atomic number 13) found abundantly in the Earth’s crust. I often describe it as the “Swiss Army knife” of metals—versatile, durable, and ready for countless tasks. Thanks to its low density (2.70 g/cm³) and remarkable tensile strength (up to 700 MPa in certain alloys), aluminum shines where weight savings and robustness are critical. Moreover, it forms a self-healing oxide layer, granting outstanding corrosion resistance.
2. Historical Evolution of Aluminum Use
Although identified in 1825, aluminum remained a laboratory curiosity until the late 19th century. In 1886, the Hall–Héroult process revolutionized production, dropping costs drastically. By 1908, the first aluminum beverage can hit the market—ushering in a new era of packaging. Since then, production has skyrocketed: global primary aluminum output reached 67.4 million metric tons in 2023, reflecting its integral role in modern life.
3. Construction and Infrastructure Applications
In construction, aluminum’s lightweight nature facilitates easier handling and reduces structural loads. I’ve seen curtain walls, window frames, roofing sheets, and cladding all benefit. For example:
Application | Benefit | Typical Alloy |
---|---|---|
Window Frames | Thermal efficiency, slim sightlines | 6063-T6 |
Roofing Panels | Corrosion resistance, low maintenance | 5005-H34 |
Curtain Walls | High strength, design flexibility | 6061-T5 |
Aluminum’s reflectivity also enhances daylighting, cutting energy costs. However, careful specification per ASTM B221 and EN 755-2 ensures performance consistency²².
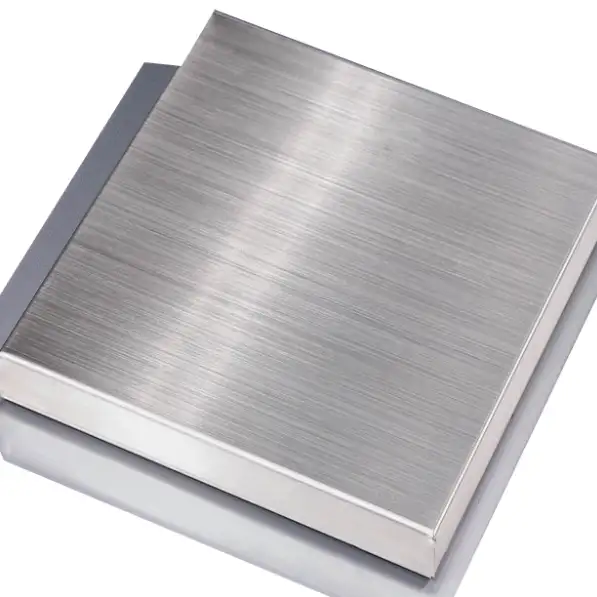
4. Packaging Industry: From Cans to Foils
Aluminum foil and cans dominate packaging due to formability and barrier properties. I often marvel at how foil—just 0.02 mm thick—locks in freshness. In beverage cans, 250 ml of aluminum saves 1.4 g of material compared to steel, reducing transport weight by 8%³³. Transitioning seamlessly between sheet and foil, aluminum is a packaging workhorse.
5. Transportation: Automotive, Aerospace, and Rail
Weight reduction is key to fuel efficiency. Automakers are substituting steel with aluminum—up to 17% of a vehicle’s body may be aluminum today. In aerospace, primary structural components comprise 50–60% aluminum alloys, notably 2024-T3 and 7075-T6, thanks to their high fatigue resistance. High-speed trains use extruded aluminum profiles for car bodies, slashing mass without compromising safety.
6. Electrical and Electronics: Conductivity in Action
Although copper beats aluminum in conductivity, aluminum’s low cost and density make it ideal for overhead power lines: a conductor weighing 100 kg can carry the same current as a 164 kg copper line. In electronics, heat sinks and enclosures exploit aluminum’s thermal conductivity (235 W/m·K)⁴⁴ to dissipate heat efficiently.
7. Consumer Goods and Household Items
Everyday objects benefit: from smartphones (light chassis) to cookware (even heat distribution). I’ve held laptops with precision-machined aluminum bodies that feel premium and withstand daily wear. Kitchenware made from 3003-H14 alloy offers both formability and food-safety compliance.
8. Industrial Machinery and Equipment
Aluminum gears, pumps, and housings reduce inertia and support high-speed operation. In marine settings—where corrosion runs rampant—I’ve specified 5083-H116 alloy for ship superstructures. Its weldability and seawater resistance meet stringent marine standards (ISO 9223).
9. Building Green: Sustainability and Recycling
Aluminum is infinitely recyclable—requiring just 5% of the energy used for primary production. Today, 75% of all aluminum ever produced is still in use⁵⁵. This circularity is a “game-changer” for sustainable design. Moreover, recycled content calms environmental scrutiny in LEED-certified projects.
10. Comparative Analysis: Aluminum vs. Competing Materials
Property | Aluminum | Steel | Copper | Plastic (PET) |
---|---|---|---|---|
Density (g/cm³) | 2.70 | 7.85 | 8.96 | 1.38 |
Tensile Strength (MPa) | 310–700 | 400–550 | 210 | 60–100 |
Thermal Conductivity (W/m·K) | 235 | 50 | 401 | 0.15 |
Recyclability (%) | 100 | 100 | 100 | ~30 |
This table underlines aluminum’s balanced profile: lightweight yet strong, highly conductive, and a recycling champion.
11. Case Study: Aluminum in High-Speed Rail Carriages
Project: CityLink Express, 2022–2024
Objective: Develop a 350 km/h train with reduced energy consumption.
Solution: Extruded aluminum body shells (6063-T6) and roof modules (6082-T6).
Outcome: 15% weight reduction, 8% lower energy use per passenger-km. Passenger feedback cited “quiet ride” and “smooth acceleration.”
This real-world example illustrates how aluminum alloys can deliver both operational efficiency and passenger comfort.
12. Technical Standards and Quality Requirements
Aluminum products must comply with rigorous specifications:
-
ASTM B209 – Aluminum and Aluminum-Alloy Sheet and Plate.
-
EN 573-3 – Chemical Composition and Form of Wrought Products.
-
ISO 6361 – Rolled Aluminium for General Engineering Purposes.
-
AA 6061 – Mechanical Properties per Aluminum Association.
Strict adherence guarantees consistent performance across global supply chains.
13. Emerging Trends and Future Prospects
Looking ahead, additive manufacturing (AM) with aluminum powders (AlSi10Mg) is gaining traction. Also, nanostructured coatings are enhancing surface hardness. Will graphene–aluminum composites become mainstream? Perhaps. The metal’s versatility ensures it remains at the forefront of materials innovation.
14. Frequently Asked Questions
1. What makes aluminum corrosion-resistant?
Aluminum forms a thin oxide layer (Al₂O₃) that self-heals when scratched, blocking further oxidation.
2. Can aluminum be welded easily?
Yes—most alloys (e.g., 6061, 5083) offer excellent weldability via MIG, TIG, or friction stir methods.
3. How does recycled aluminum quality compare to primary?
Recycled aluminum retains 95–98% of the original properties if processed correctly in closed-loop systems.
4. Are aluminum cooking utensils safe?
When anodized or coated, aluminum cookware meets food-safety standards and resists leaching.
5. What’s the lifespan of aluminum roofing?
Properly coated aluminum roofing can last 40–60 years with minimal maintenance.